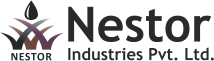
NYLOFIX-RN is a acid stable polyamide dye fixing agent dyed with metal complex and acid dyes.
Add Nylofix-RN into the bath, adjust the pH to 4.5 – 5 (with acetic acid or formic acid), and treat at 50- 55ºC for 30 mins.
Appearance : Dark brown clear liquid
Composition : Polyphenolic type condensate
Ionic nature : Anionic
pH (2% in distilled water) : 7.0 ± 1.0
Miscibility in water : Miscible
Important Note:
Substrates which are to be laminated or coated with foam should not be after treated with condensation products of the Nylofix-RN type as this impairs adhesion.
Improvement in fastness properties with Nylofix-RN:
Improving the wet fastness properties of basic dyeable polyamide dyed with cationic dyes.
Application
The wet fastness properties of anionic modified polyamide dyed with cationic dyes can be improved by after treatment with
Nylofix-RN : 1 - 3 %
pH (with acetic acid) : 5.0 – 6.0
Temperature : 50 - 60°C
Time : 20 -30 mins
General:
When dyeing polyamide /cellulosic blends in the one bath or one bath two-step process, Nylofix-RN can be used a reserving agent to prevent direct dyes staining the polyamide component.
Amount required:
Dye with an addition
- Nylofix-RN : 0.5 – 0.75 %
Method:
Because of the excellent reserving effect of Nylofix-RN on special dye selection is necessary. However, its reserving action may be reduced if non-ionic leveling agents are use.
Resist printing of PA carpets:
One-step method Wet-in-Wet
Print : white or colored resist
Nylofix-RN : 4 -12 g/l
Intermediate steaming apply colorants by pouring steam, wash – off, dry.
Important Note:
Substrates which are to be laminated or coated with foam should not be after treated with condensation products of the Nylofix-RN type as this impairs adhesion.
Improvement in fastness properties with Nylofix-RN:
Improving the wet fastness properties of basic dyeable polyamide dyed with cationic dyes.
Application
The wet fastness properties of anionic modified polyamide dyed with cationic dyes can be improved by after treatment with
General:
When dyeing polyamide /cellulosic blends in the one bath or one bath two-step process, Nylofix-RNcan be used a reserving agent to prevent direct dyes staining the polyamide component.
Amount required:
Dye with an addition
- Nylofix-RN : 0.5 – 0.75 %
Method:
Because of the excellent reserving effect of Nylofix-RN on special dye selection is necessary. However, its reserving action may be reduced if non-ionic leveling agents are use.
Resist printing of PA carpets:
One-step method Wet-in-Wet
Print : white or colored resist
Nylofix-RN : 4 -12 g/l
Intermediate steaming apply colorants by pouring steam, wash – off, dry.
Print : white or colored resist
Nylofix-RN : 4 -12 g/l
Steam, wash – off, dry.
Apply Nylofix-RN after alkaline after scouring of print, a cationic scouring agent like Altrasperse-SW, before after treatment, set a cold bath with,
To remove any residue of the cationic scouring agent and any loose anionic dye from the substrate, then after treat with,
In continuous after treatment, e.g. padding (dry-on-wet or wet-on-wet) this should be regulated through liquor pick-up
NESTOCAT – NF |
Dye Fixing Agent For Cellulosic |
NESTOCAT – NF is non formal dye fixing agent for improving wet fastness of direct and reactive dyes on cellulosics. |
NyloFix – EC Conc |
Non Formal Dye Fixing Agent for Polyamide |
NyloFix – EC Conc is non formaldehyde dye fixing agent for polyamide improves fastness properties of polyamides. |